Boat Trailer Jack Stand and Wheel Maintenance
In this video I do a bit of maintenance on the trailer jack caster wheels from our boat trailers. When they start to corrode and become hard to turn it's a good time to disassemble, clean and grease them.
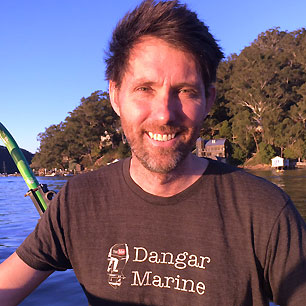
About Dangar Marine
MarineEngine.com proudly sponsors the Dangar Marine YouTube Channel. Our friend Dangar Stu draws on his experience as a commercial boat skipper and mechanic to make some great how-to videos. Dangar Marine videos cover a range of relevant topics in outboard repair, boat repair/upgrades and seamanship. Subscribe on YouTube to be notified when new videos are released.Boat Trailer Jack Stand and Wheel Maintenance – Video Transcript
Hey there, Dangar Stu here. Today's video is on trailer jockey wheel maintenance and is proudly sponsored by MarineEngine.com.
So somehow we end up always with lots of trouble with jockey wheels, we get to the point where the wheel itself doesn't rotate very well when you're trying to maneuver the trailer around the wheel just drags sideways and you flat spot it. Although I've been spraying this and it started to free up a little bit, you can see down here the handles moving with it and it's only when you can move the handle independently of the wheel that you can wind it up and down so it's pretty seized. Now given our kind of lack of time and Inclination to do a lot of maintenance on these we thought we'd pull this apart first and look inside and see whether we can clean it up and get it going again because they're about 70 bucks each so they're not super cheap.
In the top of the handle here there's a roll pin that holds it in so I'm going to push that through, get the handle off and see if we can just get the whole thing apart. Roll pins are also called spring pins depending on where you're from and either way you just punch them through, so there the pin came out pretty much intact and you can see it's just got that seam along the center so it sort of springs together and it can push out. With this one you get a little bit of independent movement, it spins and I can move the handle within a certain arc whilst holding the wheel still but no luck so what I'm thinking I'm going to do is actually put this bottom section here in the vise so I can really try and get that handle turning. It's possibly fair to say this one's a bit too far gone.
I think if I put a bar on it I'm actually just going to bend it. What I'm going to do is put this one aside and actually get a reasonably new one off another trailer. It's not in very bad condition but it's already starting to show signs of going this way so I'll use this one. Maybe once we have a look at how it works inside we can develop a strategy for pulling the other one apart. Here's the new one - it's a very similar design, the backing plate here looks identical but it has a much smaller wheel. I always think larger wheels are great, you know they run over obstacles easier but other than that they're pretty similar. Now sometimes with these if you wind them all the way extended this section actually sort of just drops out. Sometimes people do it accidentally, this one seems to hit a stop before it comes out . So I'm going to knock the spring pin out again or roll pin and see if we can then just pull the whole assembly down.
You can see already that other handle didn't come off at all, I actually gave it quite a bit of a yank. Every part of that other one's pretty corroded. Let's take this to the bench, the lights better there. What we've got at the top here is a little bearing that the weight of the trailer essentially rests on so that obviously has to pivot. I'll show you that with the jockey wheel disassembled now starting at the very top you can see there's a section where the threads have been ground off and that's because the inside of the handle is keyed. It's that key way or that key shape that allows us to turn the handle and the roll pin just stops it from pulling off the top. There's a little simple bearing, there's a washer below it or a race it actually has a groove in it for the ball bearings to roll in and then a little bushing in the top. This little plate it runs on is welded onto the shaft. The other race washer goes on top of the bearing and seats in the jack tube.
What you really can't see in the camera Is corrosion in here and resistance on this side that stops the wheel from turning when you're maneuvering the trailer and that to be honest with you is a bigger problem. By a bigger problem I mean it's something we get more frequently because it is a large surface area of metal to have corrosion on it. Because this section is slightly sealed internally the worm drive in here gets corroded less frequently. To be honest with you even if you can't wind it up and down you can still flip it 90 degrees so as a result I'm not so worried about this corrosion. I do still think it's worth looking at trying to solve. You can see this section here is kind of crimped. What I would like to do maybe is sacrifice that one that's completely cactus anyway, cut it open and just have a look at how this mechanism works. That might give us some ideas about how to save this one from ending up the same way.
What I'm going to do first is get a pry bar and just pry this handle off, it's quite seized but it might come off alright. There we go, okay. I'm going to cut this end off and then we'll take the bits over to the bench. This one feels like it's got the two races, they've got the same grooves but there's no sign of a bearing left. This is the other casing that I cut initially through near the top and then split down so I could open it and get it off. All this really is some crimp sections that lock into a groove here on this female section. If I grab this old jockey wheel you can see it's all this stuff that really sticks it together. We've tried a few different products to try and prevent this and I can see here it's actually got a lot of dust in it too. I think as you drive, dust gets into the lubricant and the lubricant itself becomes more of a glue. We've tried thin things, we've tried thicker things and I must be honest one of the things that worked the best was PB Blaster but it's very, very hard to find in Australia. Oddly you just don't seem to be able get it in shops, but it did work quite well.
Now from a maintenance point of view, I actually didn't have to cut this to take this out I just took the handle off and I dropped it down. I could take this over to a wire wheel. I'd get all the gunk off maybe take some of the galvanize off as well, which isn't great but I could clean this up. Then perhaps use a large diameter wire brush to clean up the center section. Maybe we're back in action with regards to these larger surfaces that allow the wheel to turn. I'm thinking perhaps the idea is just to pull it apart, maybe coat it with a grease like a waterproof lithium grease, reassemble it and then just periodically take it apart. It's a little bit hard to flush, you can kind of flush it if you turn it upside down. Then we put this back together. Once it's upside down you can actually get some water and spray inside here and clean it out a little bit and maintain periodically. I could put a grease nipple near the top of this outer part, put it in quite shallow so it doesn't affect the intersection rotating or scraping on it. I'm not one hundred percent sure whether you're going to get a very good distribution of the grease though., Maybe the answer here is just to disassemble it, manually apply grease to both surfaces and put it back together. Periodically clean it and re-grease it.
It's now many days later and I just remembered what we're talking about. To say this week hasn't quite gone to plan would be an understatement, but anyway. Looking at this reasonably new jockey wheel it turns out they don't really put much grease on from the factory, and pretty soon they end up like this. I don't think this one's ever going to turn again, not without a lot of effort anyway and it's probably only a year or so old. I had to check around about the best way to grease these and we couldn't really come to any sort of agreement. There's a few ways to go, one is you can disassemble it, just grease it, put it back together and see how it goes. I think there's a lot of merit in that. Disassembling it to this stage is pretty straightforward, you know you pop that roll pin, take the handle off, and you can pull it apart and it allows you to get grease to most of the critical areas, it allows you to grease the bearing at the top, it allows you to clean and grease the entire length of the intersection and maybe with a bit of rag or something grease the inside of the tube as well. We can also grease pretty much the whole length of the threaded rod, so really without installing a grease nipple we can do a pretty good job of trying to prevent this corrosion from happening in the first place.
Now because not all greases are compatible the first thing I do is take all the old grease off, as much of as I can anyway. Although we do want to get lots of new grease on, what we don't want is those two greases sort of being incompatible clashing with each other and ending up becoming more of an adhesive than a grease. So start the cleaning, if I had a large bore brush I think that would be ideal for cleaning this section but I don't. I'm just going to go with some sort of rag to clean this up with some standard, just heavy duty degreaser rather than something like a carb cleaner that I would use to get some really hard grease off. The reason for that is it's not that old so the grease is quite soft and I don't want to damage that gal coating on the metal, I want to keep that as intact as I can. Because this grease is a little bit in the threads I'll use a brush to try and get the bulk of it out. I don't think a small amount of residual grease is going to you have a huge effect, but getting the bulk is definitely going to help. All right now everything's cleaned up, let's go find some grease.
So this grease is a lithium base grease with PTFE which is essentially Teflon and now the jockey wheel itself is clean we know we're not going to have any issues with it clashing with whatever that old grease was. This grease is advertised as being used for boat trailer bearings, so I think it's the right way to go. Just quickly I'm actually going to pop these bearing races on the wire wheel because you can see here they've already got a bit of corrosion on them, they're literally weeks old so they're not the best stainless steel or anything like that. I'll quickly go and clean these up and then we'll grease them. Alright, I didn't go to town on these because once again if they are just steel with a bit of gal on them I don't want to take all the gal off, but just get that surface rust off. I think it's a good idea. With this somewhat cheaper nasty bearing, I'm just going to push the grease right through until it comes out the other side, same way you sort of pack a normal bearing. This is what the bearing looks like now with the grease pushed right in between the ball bearings and the retainer and the cage. Messy, but functionally better. Now while I've got grease all over my hands I'm just going to wipe the excess on this thread and the shaft of this.
So, this thread seizing is what's been giving us trouble winding the extension up and down and then corrosion around the main part here is what gives us trouble with the jockey wheel spinning when you're pushing the boat around the yard. That gets particularly annoying because you end up dragging and you flat spot the wheel. You know we don't need that. There's way too much greasing of cylindrical objects on this channel. All right I'm going to put this somewhere clean, particularly given how much trouble I got in in my trailer bearing video for using a dirty brake pad, It's a long story. As for the inside of the tube I think I will just put a little bit on this rag, well I say a little bit, a lot. Once again, just pushed up the tube it'll get a little bit on there. I guess I could do that a couple of times just to make sure. Now to reassemble it I'm just going to put my bottom race on here, bearing itself then the top race. Then there's just a little kind of PVC nylon spacer that went in between just to keep them centered on the shaft.
Drop the handle back on then I'll just hammer the roll pin back through to hold it all together. There's no great trick to getting these roll pins back in because the top of the shafts actually keyed, you can see there's a flat section on the bottom here which means once you drop this on the holes are all lined up. Anyway, that's it really. Now I'm just going to wind it all the way down, certainly feels better already that's for sure. All right now I'm just going to get rid of this excess grease and then we'll talk about a few provisos. With this setup, the main thing that concerns me is trying to keep the wheel lowered as much as possible. Grease is awesome when it's in between two layers inside a sealed bearing all this kind of stuff, but it does attract dirt so if you have your wheel extended the whole time the grease dries out dust flows onto it. That grease will actually attract that dirt and hold it in and become kind like a putty and possibly make it worse. If you leave the trailer extended up a lot. There are maybe things you could try other than grease.
You could try tetryl which is a sort of a rust inhibitor sort of thing, you could try like a PB Blaster, that kind of thing. So I think maybe there were some sprays because you're going to access that area you can raise it, clean it, respray it, keep it going. I've tried that in the past and I haven't had a lot of luck and that's why I'm willing to give grease a go now to Compare. I am very happy though having grease on that threaded section, I'm happy having the bearing heavily greased all that kind of stuff. I'm very comfortable with it because inside the unit it won't get dust on it really and hopefully it'll stop the saltwater from getting to the middle. Because this one is pretty much unrecoverable now, it's pretty locked solid, my other thought is if it starts going wrong, if it starts feeling stiff it's not that hard pull it apart clean it re-grease it. Good to go again.
So if you start getting that feeling like it's not as smooth as it used to be, jumping on it quickly is going to help you rather than just letting it slide. The great thing about servicing these is it doesn't take any special tools other than maybe a punch to get the roll pin out and it certainly doesn't take a lot of time. Well thanks for watching. I hope this video actually helps you. I know it's not rocket science and not particularly interesting in some ways but we've had a lot of trouble with these and I'm hoping we can have less trouble in the future because of a bit of maintenance. Because we've got our meetup coming up soon I've got a few life jackets I'm going try and bring back to life so I'll do a video on that soon. I've also bought a tacho and a solar cell and controller for the green machine so we'll be installing those soon as well. All right well take care and I'll catch you soon. See ya!